Behind The Product: ENVE Carbon Road Hub
For over a decade, ENVE has focused its carbon expertise on crafted carbon rims, and partnered with the industry’s most reputable hub manufactures to bring them to life – delivering a better ride experience to performance oriented road riders around the globe.
The introduction of the all new redesigned Carbon Road Hub solidifies ENVE’s transformation from rim to wheel manufacturer and elevates our wheel performance to an all-time high, while at the same time allowing us to offer more competitive wheelset pricing as a result of this investment in proprietary ENVE hub technologies.
While this isn’t our first branded road hub, the latest ENVE Carbon Road Hub is the first hub that is 100% ENVE inside and out, whereas the previous generation hub (2015-2017) featured internals sourced from a competing manufacturer. The decision to source internals was strategic as it allowed us to focus design efforts on a hub shell concept that to date, had not yet been executed against in a reliable every day rideable manner. While the first generation hub achieved its objectives for being lightweight, strong, and reliable it was not without its shortcomings.
The latest ENVE Carbon Road Hub builds on its predecessor’s strengths, and addresses its weaknesses by delivering more value, features and performance that meet and exceed those of the world’s leading hubs.
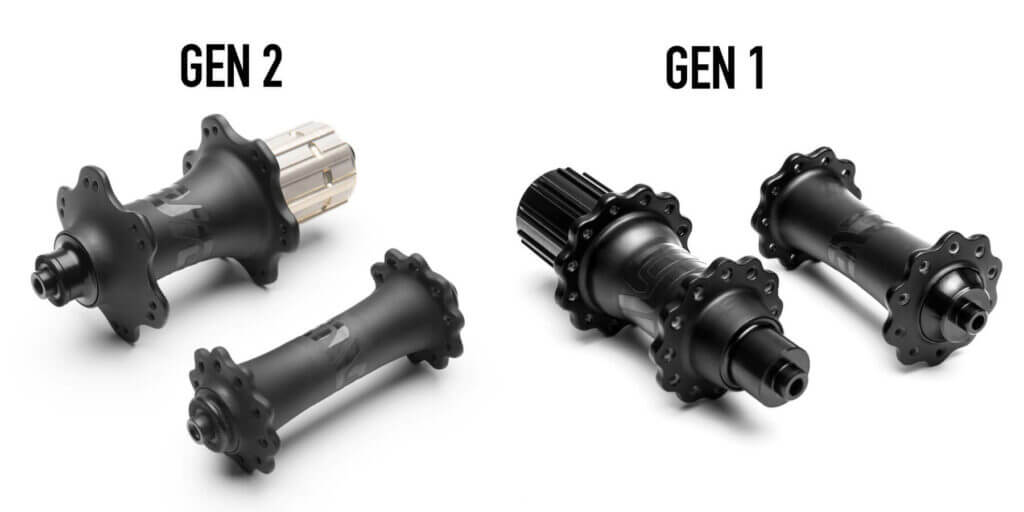

THE HUB SHELL
While utilizing carbon in a hub shell isn’t a particularly novel concept, molding it all in a one-piece design is. Most typically, carbon is used in hubs by bonding a carbon tube as a bridge between two alloy flanges. This type of construction is ultimately a strategy used when attempting to reduce the weight of an alloy hubset.
By molding the entire hub shell from carbon, you can achieve substantial weight savings without sacrificing the hub’s geometry. Conversely, if you want to make a lightweight alloy hub, you need to reduce the weight of the hub shell which requires compromising the hub’s geometry in the name of weight savings.
While all hub manufacturers are faced with making these decisions, our carbon expertise has created a hub shell that reduces these tradeoffs between weight savings and geometry better than any other hub shell on the market. As proof, the ENVE Carbon Road Hub weighs 252 grams per hubset and features a 55mm rear hub flange diameter while for comparison’s sake, a DT Swiss 180 features a hybrid alloy/carbon hub shell with a 45mm rear hub flange diameter and weighs 283 grams per hubset.
Much of what makes the full-carbon hub shell possible is the inclusion of our patented Molded Spoke Hole Technology in the hub flanges. To understand this technology, it is important to understand some basic properties of carbon fiber. For ENVE, carbon fiber is our material of choice whenever its use can be justified. The reason we choose carbon is for its unique tensile strength (ability to carry load under tension), lightweight, toughness, and its ability to be tuned for the demands of the final product. Given carbon’s unprecedented ability to support loads under tension, it is the perfect material for supporting spoke tension in both the rim and hub flange. The one caveat is that in order for carbon’s true potential to be achieved, the fibers must run continuously and uninterrupted. If the fibers are cut, the tensile properties of the fiber are eliminated. Uninterrupted carbon fibers are the backbone of the molded in spoke hole technology.

Like ENVE rims, each spoke hole in the flange of the Carbon Road Hub is molded-in. This technology saves weight while at the same time creating a spoke hole that is incredibly strong. When compared to the first generation carbon road hub, the spoke holes in the new carbon road hub are 14% stronger, withstanding loads averaging 790 lbs.
In addition to molding in the spoke holes, the diameter and width of the spoke holes have been further refined to improve the fatigue at the spoke head/hub flange intersection by 67%. This data point ensures greater reliability, and confidence in the hub and spokes for the rider as the miles are piled onto their wheelset. The ENVE Carbon Road Hub is designed for use with j-bend type spokes for their ability to deliver a more reliable wheel build and that replacement spokes are generally readily available should an unfortunate spoke failure occur.
Finally, to further reduce the weight of the hub shell, all excess material is removed from between the spoke holes creating the familiar scalloped flange shape of an ENVE hub.
THE HUB GEOMETRY
Wheels are highly complex and often underappreciated in their complexity. First, you have the rim which has to be lightweight and manage rider weight, impacts, airflow, tire pressure, and spoke tension. Then consider that the best rim in the world, if laced to a mediocre hub with compromised spacing and flange geometry, will result in a mediocre wheelset. Nothing on the bike is more complex and dynamic.
For the reasons above, we found it necessary to take control of our own destiny by developing a hub that enhances versus diminishes the performance of an ENVE wheelset. So what, does an enhanced ENVE wheelset feel like on the road? Essentially, faster accelerations, and more confident handling when sprinting, standing, or cornering.

Here’s how the hub geometry has been refined to out-perform the leading aftermarket hubset, and elevate the performance of complete ENVE wheelsets.

The next generation Carbon Road Hub utilizes a paired spoke hole pattern which improves tangency of the spoke angle to the rim by creating what we refer to as a virtual three-cross lacing pattern. The flange diameter itself has been increased from 45mm to 55mm with no weight penalties to maximize torsional stiffness. In the real world this means greater response and efficiency under the most aggressive accelerations.
UNPRECEDENTED RELIABILITY – AXLES, BEARINGS, AND MORE
When asked, “What do you value most in a hubset?” the market came back with a resounding response for “reliability.” With that knowledge, we spared no expense in ensuring that the Carbon Road Hub become the gold standard in reliability. The extreme strength and lightweight of the carbon hub shell allows for the use of robust axles and internals where others are forced with the hard decision of adding weight or compromising long term reliability.
The ENVE Carbon Road Hub features a robust 17mm rear axle and a 10mm front axle. The large rear axle diameter reduces flex, improves drive train efficiency, and helps prolong bearing life. On the front hub, a 10mm axle is capped with stainless steel end caps to ensure durability and a long service life.

In the same way that a mediocre hub can bring down a world-class rim, a high maintenance or otherwise underperforming bearing can bring down what would otherwise be a best in class hubset. For this reason the Carbon Road Hub comes spec’d with custom premium grade stainless steel bearings. Those familiar with the original ENVE carbon road hub know that it included ceramic bearings. While ceramic bearings are capable of delivering extremely low rolling resistance and therefore high levels of efficiency, this is primarily achieved by using non-contact bearing seals that eliminate friction between the bearing race and its seal. While fast for the moment, this bearing setup is readily contaminated and if not maintained, bearing performance can be compromised in one ride through harsh weather conditions.
It is our opinion that the stainless steel bearing spec’d in the Carbon Road Hub is an upgrade over the first generation’s ceramic bearing both in terms of rolling efficiency and long term reliability. To achieve a balance of long term reliability and efficiency contact bearing seals are used anywhere a bearing is exposed to the elements while non-contact type bearing seals are used on all internal bearing faces.

In testing, the stainless steel bearings rolled fast and smooth for literally thousands of miles beyond what the best ceramic bearings were capable of. Additionally, the use of stainless steel means that for cyclists living near the coast, in high humidity, or frequently riding in the rain, your bearings will resist corrosion and look beautiful for years beyond what a traditional bearing is capable of.
PERFECT PRELOAD™
If there was one complaint heard more than any other over the years about hubs it’s that, “My bearings have play in them.” Bearing play is a result of inadequate pre-load on the bearing or sloppy tolerances. Essentially, you have your hub shell, axles, bearings, and it all needs to be compressed together just enough so that there is no play and drag. There are a couple common ways of doing this. The first is a basic stack up, and DT Swiss is an example of this. With this design, one presses everything together and the design’s tolerances deliver the desired performance. This method requires precision machining to ensure everything “stacks up” correctly. It is possible for this design to work, as proven by DT, but with time, any imperfections in the stack up will be magnified by way of accelerated bearing fatigue and diminished performance. The beauty of this design is the simplicity, the down side is bearing life.
A more common and forgiving way of managing bearing pre-load is to design the hub with an adjustable pre-load tension feature like a lock ring. This is a proven way of managing bearing pre-load, but is not without its flaws. First, if you need to adjust bearing pre-load, you’re going to need a tool and it’s more often than not a size not readily handy on your multi-tool. If bearing play is permitted to go unattended to, one can permanently damage the hub making it impossible to achieve optimal hub performance without replacing costly components of the hub. The other problem is that of over-tightening your pre-load. If over-tightened, you will certainly not have bearing play, but now you’ve increased drag on the bearings which in turn reduces efficiency and costs valuable energy.
Our goal was to solve the problems associated with bearing pre-load and Perfect Preload™ is the solution.

Perfect Preload™ promises to maintain optimal preload on the bearings for the service life of the hub. Bearing preload is achieved via a calibrated wave washer and snap ring. The wave washer sits between the bearing and a snap ring installed on the axle. This system produces a consistent and dynamic pre-load setting that eliminates bearing slop and the need for riders to adjust pre-load. Because pre-load is optimized and fixed, bearing performance is maximized, reducing premature bearing wear.
DRIVE MECHANISM
When developing a new hub that must meet “best-in-class” performance metrics, it goes without saying that the drive system is figuratively and literally responsible for setting the tone of the entire product. The Carbon Road Hub features a 40t ratchet with 9 degrees of engagement and strikes a fine balance between responsiveness and long term reliability. When ratchet type drive systems with tooth counts greater than 40t were tested, reliability was diminished exponentially.

ENVE researched and tested competing drive system designs ranging from pawl to ratchet type systems and ultimately decided upon a ratchet type system for reasons associated with weight savings, efficiency, reliability, and ride tester feedback. Additionally, the ENVE ratchet design minimizes the number of small parts in the system to the drive ratchet, freehub ratchet and a single spring. The ratchet type design delivers maximum weight savings, reliability, and ride testers preferred the ride feel and acoustics over other designs.
Finally, the freehub driver body is machined from 7075 aluminum alloy, and hard anodized for durability. The ENVE Carbon Road Hub is compatible with Shimano, SRAM, and Campagnolo drivetrains by simply exchanging the freehub body – no re-dish is required.
CONCLUSION
Our investment in proprietary hub technologies has allowed us to further optimize a wheelset to deliver more value, ride performance, reliability, weight savings, and confidence. Ultimately, the Carbon Road Hub ushers in a new era for ENVE where proprietary rim and hub technologies intersect, raising the bar for road bike wheelset performance into the future.
